Mejora de una línea de producción
Estudio mediante el programa WItness de la mejora de una línea de producción.
2/7/20245 min leer
INTRODUCCIÓN
Presentación y justificación
La empresa textil nos propone el estudio de una de sus líneas productivas, en concreto, la línea de sellado y estampación de camisetas.
Objetivos
Los objetivos del trabajo consisten en evaluar la eficiencia de la línea productiva, a partir de los siguientes indicadores:
Evaluación de los tiempos de procesado, tanto el global para producir 150 pedidos, como el tiempo medio que pasa un pedido en el sistema.
Detección de cuellos de botella en la línea de producción escogida, mediante el análisis de la ocupación de las diferentes máquinas.
Estudio de la ocupación de los almacenes.
Además, se propone una mejora basada en el análisis de los indicadores del sistema actual.
Alcance
El alcance del estudio va desde que la camiseta tintada entra al almacén de entrada de la fábrica hasta que esta sale de las líneas de estampado y sellado.
DESCRIPCIÓN DEL SISTEMA
La línea de producción está compuesta por cuatro máquinas, un sistema de control de calidad, una transpaleta y de diferentes almacenes que hacen de conexión entre las máquinas. (Figura 1).
La línea tiene una única entrada, un almacén inicial donde se produce la recepción de lotes. Los lotes de camisetas vienen en pedidos de diferentes cantidades, que van desde las 20 hasta las 500, pero todas corresponden a un mismo tallaje, color, dibujo y marca. El lote completo se somete a un control de calidad realizado por un único operario, que descarta las camisetas defectuosas y clasifica los pedidos. En concreto, la empresa trabaja con dos marcas, X e Y, que se derivarán posteriormente al proceso de sublimación o serigrafía respectivamente. Tras esta etapa, las camisetas quedan almacenadas en un pulmón intermedio, hasta entrar en la siguiente máquina.
Posteriormente, un operario se encarga de sellar las camisetas del pedido de una a una. Después, este queda almacenado en un segundo pulmón intermedio a la espera de ser transportado. A continuación, se deriva el lote hacia el proceso de estampación o sublimación mediante una transpaleta conducida por un operario, que se encarga de cargar el palet y transportar la carga. El 60% de los lotes corresponden a la Marca X, mientras que el 40% restante pertenecen a la Marca Y. No obstante, antes de llegar a las máquinas, los lotes se guardan en almacenes intermedios, separados por la marca, que garantizan la no obstrucción de su máquina correspondiente.
Por una parte, respecto al proceso de estampación por serigrafía, los lotes completos primero pasan por serigrafía y cuando ya tienen el dibujo, lo fijan en el horno industrial en forma de túnel. El tiempo que pasa cada lote en la máquina es proporcional a la cantidad propia del lote, ya que, las camisetas se personalizan de una en una. En el caso de la serigrafía, el proceso requiere la intervención de un equipo de operarios, mientras que el horno industrial funciona automáticamente. Finalmente, se produce la salida de las camisetas de la Marca X.
Por otra parte, respecto al proceso de sublimación con una única máquina, el tiempo que pasa cada lote en la máquina es proporcional a la cantidad propia del lote, ya que solo hay un operario encargado de ir pasando las camisetas de una en una. Por último, terminado el lote completo, se produce la salida de las camisetas de la Marca Y.
En resumen, en el siguiente diagrama puede verse el sistema descrito con los diferentes elementos.
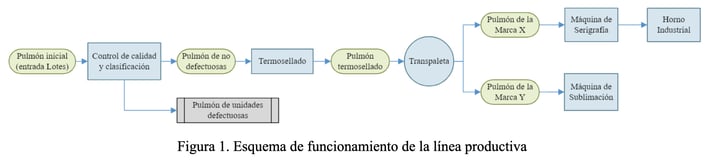
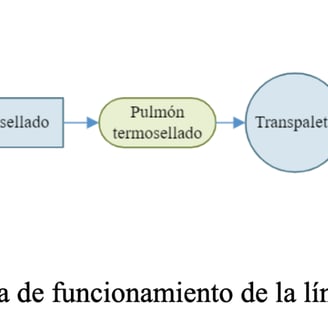
Hipótesis y cálculos
Para la simulación, se ha establecido una tiempo de llegada entre pedidos basado en una logarítmica normal de media 1,3, multiplicada por 60 min.
La recepción de pedidos está limitada, la fábrica empieza de vacío recibiendo lotes hasta llegar a 150 pedidos, momento en el que se para la venta comercial.
Las máquinas no comparten operarios, por lo que no se han representado en el modelo.
Las máquinas transforman las camisetas de una en una y los pedidos son de cantidad variable, por lo que los ciclos de las máquinas dependen de dichas cantidades.
Elementos y conexiones
Para la modelización del sistema por Witness 23.0 se utilizan minutos como unidad de tiempo.
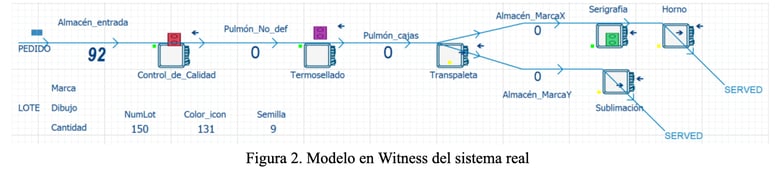
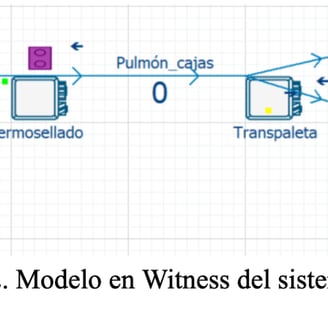
EXPERIMENTACIÓN Y RESULTADOS OBTENIDOS DEL SISTEMA
Se han realizado un total de 10 réplicas, cambiando la semilla, con el fin de evaluar el procesado de 150 pedidos, desde que entra el primer pedido con la fábrica en vacío hasta que sale el último ya terminado. Los datos obtenidos para los indicadores previamente definidos són:
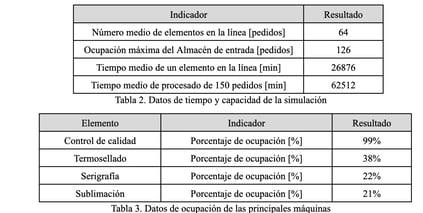
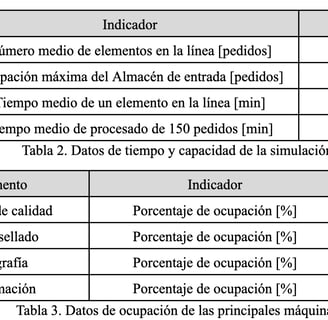
En cuanto a los resultados obtenidos, puede verse claramente que el cuello de botella se encuentra en el Control de Calidad. La máquina cuenta con una ocupación del 99%, muy por encima del resto. Esta situación provoca que en el Almacén de entrada se acumulen los pedidos a la vez que el resto de máquinas están infrautilizadas, ya que todas trabajan por debajo del 40 % de ocupación.
PROPUESTA DE FUNCIONAMIENTO ALTERNATIVO
Modo de funcionamiento alternativo
Como solución al problema detectado, se propone a la empresa que invierta en la creación de una segunda línea de Control de Calidad, contratando a un nuevo operario y colocando un segundo banco de trabajo, junto al actual, para que así puedan compartir los almacenes adyacentes.
Experimentación y análisis de resultados (comparación con modelo inicial)
Para la experimentación, se creó una segunda máquina de Control de Calidad, paralela a la ya existente, de forma que se reparte equitativamente la carga de trabajo entre las dos máquinas. Los resultados obtenidos tras las 10 mismas réplicas que en el apartado anterior són:
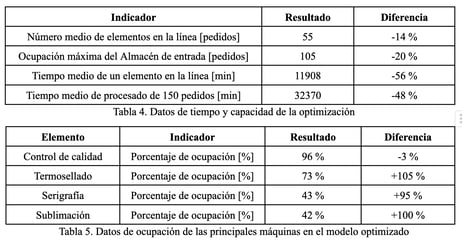
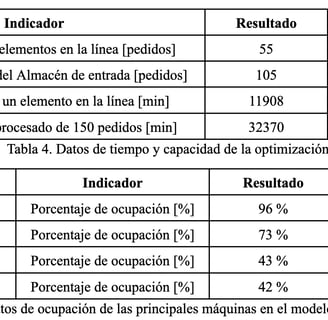
Tras la mejora propuesta, se observó una reducción significativa de los tiempos de trabajo. El tiempo de procesamiento promedio de un pedido se optimizó en un 56 % y el tiempo total para completar 150 pedidos se redujo en un 48%. Simplemente duplicando la estación de control de calidad, se ha reducido el tiempo total de producción de 26 a 11,2 semanas laborales.
Esta mejora también ayudó a reducir la acumulación de pedidos en la línea y la ocupación del almacén inicial, disminuyendo un 14% y un 20% respectivamente. Asimismo, se ha observado un aumento significativo de la ocupación del resto de máquinas, en algunos casos incrementando el tiempo de actividad del equipo hasta en un 105%, aumentando la eficiencia total del sistema.
CONCLUSIONES
Al inicio del estudio, la línea de producción textil trabajaba en una situación claramente ineficiente. La etapa de Control de Calidad estaba afectando gravemente a la acumulación de pedidos en la entrada y retrasando los tiempos productivos de la línea. Además, el resto de máquinas estaban trabajando muy por debajo de sus capacidades.
Sin embargo, ha quedado demostrado que con una pequeña inversión añadiendo una segunda línea de Control de Calidad, la eficiencia global de la línea aumenta significativamente, disminuyendo en más de la mitad el tiempo productivo y rentabilizando en un 100% más el uso de la maquinaría.